The Famous
Leatt Lab
Based in Cape Town, South Africa, this is Leatt®’s home of research & development. Here Dr. Leatt and his team of engineers and designers conceptualise and test new products and constantly strive to improve existing products even further.
The facility features state-of-the-art testing and prototyping equipment that enables the team to take a product from conceptualisation, through testing, all the way to pre-production prototypes.
While the majority of Leatt®’s R&D gets done at the Cape Town facility, collaborations with international partners give our products an international flavour.
MB CHB (UCT) | Dr. Leatt
At the heart of the Leatt® Lab is Dr. Chris Leatt himself. A rider, father and inventor. Dr. Leatt was in the process of specializing in neurosurgery when he assisted in the treatment of a victim of a tragic motorcycle enduro accident. A fellow rider, Alan Selby, died on the track from a suspected neck injury. It was something Chris never wanted to see again or subject his son, aged 4 at the time (and who had just started riding) to the risks of and so he left his studies and began to design what would ultimately become the Leatt neck brace.
Born and raised in South Africa, Chris studied medicine at the University of Cape Town.
He began his internship in the UK in 1995, before returning to his home country to take up a position as General Practitioner three years later.
He has worked in the trauma wards of several hospitals, and spent time as a registrar at the Tygerberg Academic Hospital’s Department of Neurosurgery. In 2004, he gave up his medical career to focus exclusively on the Leatt neck brace.
Dr. Leatt was also a medical officer for three FIM MX South African Motorcycle Grand Prixs, and was frequently trackside during races in Nelspruit and Sun City. In 2005/ 6, he was the injury assistant officer for Motorsport South Africa (MSA).
Dr. Leatt heads up the Leatt®-Lab in Cape Town, South Africa, where most of Leatt®’s research & development takes place. He also still participates actively in motorcycle racing.
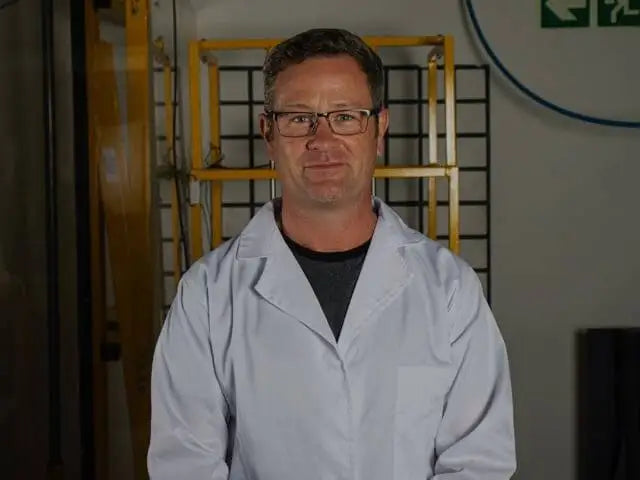
OUR PROCESS | Testing
The philosophy of testing at Leatt® has been to develop test rigs and methods that allow comprehensive in-house testing and exploration of product performance.
Using a range of real life scenarios similar to the types of situations that might be encountered in a motorcycle, bicycle, kart, automotive racing or other accident, tests are conducted at intensity levels that allow Leatt® engineers to fully understand and characterise accident dynamics and product / rider interaction, in order to optimise product performance.
It also gives Leatt® engineers the confidence to expect a first round approval when submitting product to certification facilities where appropriate for examination.
In the early innovation of the motorcycle neck brace, Dr. Leatt had no standard against which to test quality and performance, no theory to guide the design and no practical testing methods to measure the results.
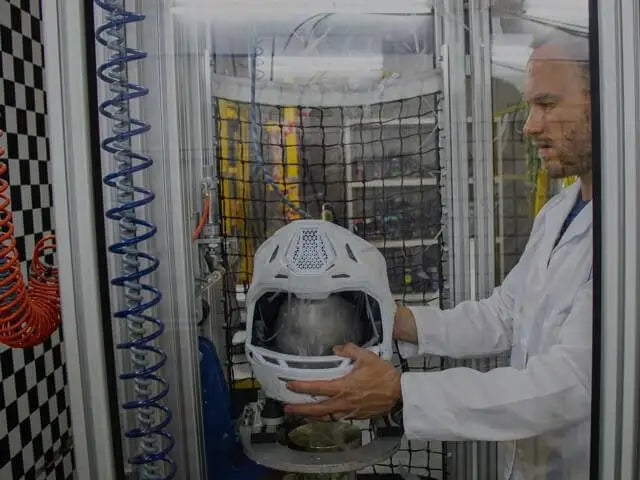
OUR PROCESS | Simulations
Extensive modelling and simulation is used in the development of products. Some of the tools used are:
- Validated H-III ATD Simulations using MSC Adams, LifeMOD™
- Detailed Spine Model using MSC Adams, LifeMOD™
- Finite Element Analysis using MSC SimOffice™ with NASTRAN
- FEA in collaboration with Strasbourg University
- FEA in collaboration with Stellenbosch University
- Mold Flow Analyses
- Helmet FEA in collaboration with Newton Test Labs
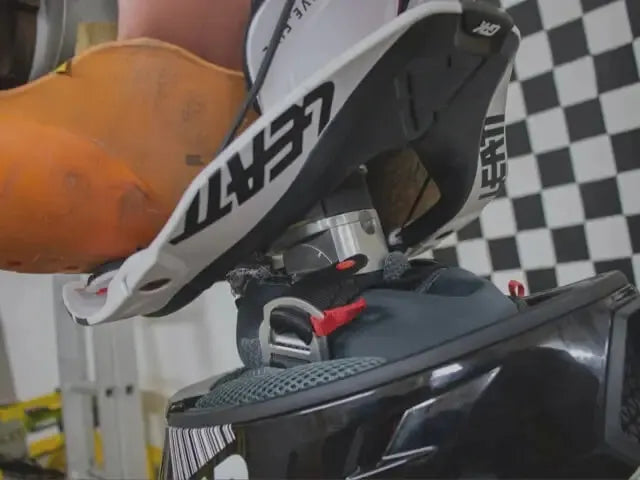
MARTIN | Our Test Dummy
Martin, our 50th percentile Hybrid III Anthropomorphic Test Dummy, is as much part of the Leatt® team as anyone. His design allows us to accurately measure many impact scenarios and provides us with test results and, more importantly, repeat and compare tests. Martin is similar to those dummies used by car manufacturers and boasts a total of some 23 built-in sensors that helps ensure valid and reliable data. In addition to this, Martin has an interchangeable Motorcycle Anthropomorphic Test Dummy (MATD) neck for non-seat belted test conditions (unrestrained torso impacts). On a regular basis, we swing him, crash him and drop him, all in the name of better, more reliable products.
These dummies are designed utilizing a wide range of materials, including rubber, foam, vinyl, aluminium and steel, to create a device with high bio fidelity. By using biomechanical data and combining more than thirty years of testing and development to improve the impact response of the test dummy, it has come to closely approximate that of humans. The Hybrid III 50th Percentile Male ATDs can accommodate a wide range of instrumentation including accelerometers, load cells and transducers from the head to the toes, making it a versatile device for compliance testing and research and development. The H-III 50th % Male ATD represents a 50th % (median) male occupant in mass and inertia and is the preferred test device for FMVSS 208 testing. It is regulated by the USA Code of Federal Regulations Part 572, Subpart E, as well as in the European ECE Regulations.
